ABS injection molding is a highly versatile and efficient manufacturing process that produces durable, high-quality plastic parts used across various industries. This method involves melting ABS resin and injecting it into a custom mold to create intricate shapes and designs. From understanding the preparation and heating phases to the final cooling and ejection of parts, the ABS injection molding process offers precision and flexibility for producing a wide range of applications. In this article, key steps, benefits, and technical considerations of Injection molding ABS are explored to help manufacturers optimize their production and achieve superior results.
What is ABS Injection Molding?
Injection molding ABS is a manufacturing process that involves the use of Acrylonitrile Butadiene Styrene (Polymer material comparison: ABS vs nylon), a versatile thermoplastic polymer, to create precise plastic parts through an injection molding technique. In this process, ABS pellets or granules are heated to a molten state and injected into a mold cavity under high pressure. Once the material cools and solidifies, the mold is removed, leaving behind a well-defined, durable plastic part.
ABS is widely used in injection molding due to its excellent balance of strength, toughness, and cost-effectiveness. It offers a range of mechanical and aesthetic properties, making it suitable for producing parts that require high impact resistance, good surface finish, and the ability to withstand moderate heat. These characteristics make ABS an ideal choice for applications in various industries, including automotive, electronics, consumer goods, and medical devices.
The process is highly efficient, allowing manufacturers to produce high volumes of parts with intricate designs in a relatively short amount of time. The flexibility of ABS injection moulding makes it one of the most popular materials for mass production of plastic components.
ABS Injection Molding Process
The ABS injection molding process is widely used for producing strong, durable, and high-quality plastic parts. Below is an overview of the key steps involved in the process, along with relevant technical data:
1. Material Preparation
ABS resin pellets, typically in the form of small granules, are first loaded into the hopper. To ensure optimal molding, the pellets are pre-dried at temperatures of around 80°C to 90°C for 2-4 hours to remove any moisture content. This is essential because moisture can cause defects such as bubbles or voids during the molding process.
2. Heating and Melting
Once the ABS pellets are in the barrel, they are heated to the required temperature for melting. The temperature is usually set between 210°C and 250°C depending on the specific grade of ABS being used. The material is gradually melted as it moves through the barrel, where it reaches a molten state suitable for injection. The screw speed and heating zones are carefully controlled to ensure the material is uniformly melted without degradation.
3. Injection into the Mold
Once the ABS material is melted, it is injected into the mold cavity under high pressure. The injection pressure typically ranges from 500 to 1500 bar (depending on part complexity and size). The mold is designed to accommodate the specific part shape, with features like cooling channels to expedite the cooling process. The molten ABS is injected quickly to ensure the mold cavity is filled evenly and to avoid air pockets.
4. Cooling and Solidification
Cooling is a critical phase where the molten ABS solidifies into its final form. The cooling time is largely determined by the thickness of the part and the design of the mold. As a general rule, cooling times can range from 15 to 90 seconds. Thicker parts will require longer cooling times to avoid warping or shrinkage. Cooling channels built into the mold help facilitate uniform temperature distribution during this stage.
5. Mold Opening and Part Ejection
Once the ABS part has cooled sufficiently, the mold is opened, and ejector pins push the solidified part out of the cavity. The cooling rate is carefully controlled to prevent defects such as warping or surface imperfections. Depending on the complexity and features of the part, multiple ejector pins might be used to ensure the part is ejected without damage.
6. Post-Processing
After ejection, parts may need post-processing, such as trimming excess material (flash), surface polishing, or secondary operations like painting or coating. For example, flash removal can be done using automatic trimming machines, or parts might be subjected to vibration finishing for smoothing edges. Post-processing ensures that the final product meets the aesthetic and functional requirements.
7. Quality Control and Inspection
Throughout the entire injection molding process, quality control is paramount. The mold temperature, injection pressure, cooling time, and material consistency are all monitored. Post-production, parts undergo visual inspections, dimensional checks, and functional tests to ensure they meet the specified tolerances and industry standards. Common methods include using a coordinate measuring machine (CMM) to check dimensions and X-ray inspection to detect internal voids.
Overview Plastic Material ABS for Injection Molding
ABS is a high-impact, rigid thermoplastic polymer that has earned a reputation for its excellent combination of strength, toughness, and versatility. It is composed of three main components: acrylonitrile, butadiene, and styrene. These components provide unique characteristics that make ABS moulding suitable for a wide range of applications, particularly in injection molding.
ABS’s popularity can be attributed to its ability to be easily molded into complex shapes and its superior resistance to impact and environmental factors. Additionally, ABS has a relatively low processing cost compared to other materials, making it a favored option for mass production.
Properties of ABS
ABS offers a unique balance of physical, chemical, and thermal properties that make it suitable for injection molding. Below is a table outlining the key properties of ABS.
Property | Description |
---|---|
Density | 1.04 – 1.06 g/cm³ (varies depending on the grade) |
Tensile Strength | 40-50 MPa |
Flexural Strength | 80-120 MPa |
Impact Resistance | High impact resistance, especially at low temperatures |
Heat Deflection Temp. | 100 – 105°C at 1.8 MPa |
Flammability | UL94 V-0 rating (varies by grade) |
Surface Finish | Smooth, glossy finish with good colorability |
Chemical Resistance | Good resistance to dilute acids, alkalis, and some oils |
Melt Flow Index | 20-40 g/10 min at 230°C with a 2.16 kg load (depending on grade) |
These properties make ABS highly versatile and adaptable for a variety of injection molding applications, ensuring its widespread use in different industries.
Advantages of ABS Plastic Injection Molding
ABS offers several benefits that make it a top choice for manufacturers. The following advantages make ABS an excellent material for injection molding:
- Durability and Impact Resistance: ABS is known for its high resistance to impact, making it ideal for products that need to withstand rough handling and stress.
- Ease of Processing: ABS can be easily processed with minimal effort, and its relatively low melt temperature allows for quicker cycle times during injection molding.
- Design Flexibility: ABS’s ability to form complex shapes with precision, combined with its ability to be easily modified with additives, provides manufacturers with the flexibility to meet specific design needs.
- Cost-Effective: Compared to other engineering plastics, ABS is relatively inexpensive, which translates into lower production costs, especially in high-volume runs.
- Aesthetic Quality: ABS offers a smooth, glossy surface that can be easily painted or finished, making it ideal for consumer-facing products that require a polished look.
- Good Thermal Stability: ABS holds up well at moderate temperatures, making it suitable for applications that require heat resistance, such as automotive parts and electrical housings.
Disadvantages of ABS Injection Moulding
While ABS is an excellent material for many applications, it does come with a few limitations that manufacturers need to consider:
- Low Resistance to UV Radiation: ABS can degrade when exposed to ultraviolet (UV) light, which can cause it to lose strength and flexibility over time. This makes it less ideal for outdoor applications unless protected with a UV-resistant coating.
- Not Suitable for High-Temperature Applications: While ABS performs well in moderate heat conditions, it is not ideal for environments exposed to extreme temperatures.
- Prone to Stress Cracking: Under certain conditions, ABS can develop stress cracks, especially when exposed to chemicals or extreme stress.
- Environmental Impact: ABS is not biodegradable, which can raise environmental concerns, particularly in large-scale plastic production.
Despite these disadvantages, ABS remains a versatile and reliable material for injection molding, with proper handling and design adjustments mitigating many of its limitations.
ABS Injection Molding Design Guidelines
Proper design is critical for ensuring the success of ABS injection molding projects. The following guidelines can help optimize the design of ABS parts for molding:
- Wall Thickness: Keep the wall thickness consistent throughout the part to ensure uniform flow and prevent warping or shrinkage. Ideal thickness is typically between 1.5mm and 3.5mm.
- Draft Angles: To ensure easy removal from the mold, incorporate a draft angle of 1 to 2 degrees on vertical surfaces.
- Radii: Use radii instead of sharp corners to reduce stress concentration and improve moldability.
- Gate Design: Proper gate placement is crucial to ensure even filling of the mold. Common gate types for ABS injection molding include edge gates, pin gates, and sub-gates.
- Venting: Ensure adequate venting to allow air to escape during the injection process, preventing air traps and incomplete filling.
- Mold Temperature: Maintain a mold temperature between 50°C and 70°C to optimize cooling times and reduce internal stresses.
- Shrinkage: ABS molded undergoes shrinkage during cooling, typically around 0.4% to 0.8%. Proper mold compensation is necessary to account for this shrinkage and achieve precise final dimensions.
Common Applications of ABS Injection Molding
ABS molding is widely used across various industries due to its versatility, durability, and cost-effectiveness. Some of the most common applications of ABS injection molding include:
Consumer Electronics: ABS is used for manufacturing housings, covers, and casings for products like mobile phones, tablets, and computers due to its toughness and excellent surface finish.

Automotive Parts: ABS is used in the production of interior and exterior automotive components, such as dashboards, bumpers, and trim parts, offering a balance of strength, heat resistance, and aesthetics.

Medical Devices: ABS is employed in making medical devices, including equipment housings and surgical tools, thanks to its stability, biocompatibility, and resistance to chemical cleaning agents.
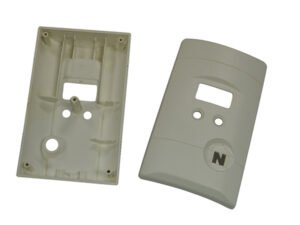
Household Appliances: ABS is found in products such as vacuum cleaners, dishwashers, and kitchen gadgets because of its durability and resistance to wear.

Toys and Sporting Goods: ABS is used in the production of toys, LEGO bricks, and sporting goods like helmets and gear due to its ability to withstand high-impact forces.

Conclusion
ABS injection molding has proven to be an effective, versatile, and cost-efficient solution for manufacturers across various industries. With its superior mechanical properties, ease of processing, and aesthetic versatility, ABS parts is well-suited for producing durable and high-quality plastic parts. By understanding the material’s properties, advantages, and design considerations, manufacturers can make the most of injection moulding ABS to produce reliable products at scale. While there are a few limitations, such as its UV sensitivity and stress-cracking tendencies, these can be addressed with appropriate material handling and design techniques. In the ever-evolving world of manufacturing, ABS continues to be a material of choice for efficient, large-volume production.