Compression molding process is a widely used manufacturing method that involves shaping materials, typically thermosetting plastics or rubber, by applying heat and pressure molding within a mold. This technique is particularly valuable for producing complex shapes and large parts efficiently. Understanding the compression molding process is essential for manufacturers as it enables them to optimize production, reduce costs, and enhance product quality. In this complete guide, we will explore the details about the compression molding process.
What is Compression Molding Process?
Compression molding process is defined as a process where a pre-measured amount of material, often in a preheated state, is placed into an open mold cavity. The mold is then closed, and heat and pressure are applied to compress the material into the desired shape. During this process, the material undergoes curing, transforming from a pliable state into a solid form that retains the mold’s configuration. This method is particularly effective for creating parts with simple geometries and larger dimensions, making it ideal for applications requiring robust components. Common examples of products made using compression molding plastic include gaskets, seals, and various automotive parts.
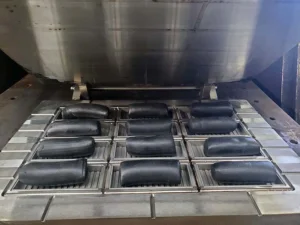
The Compression Molding Steps
The compression moulding process is a complex and detail-oriented manufacturing method. consists of several key steps that transform raw materials into finished components.
Material Preparation
The first step in the compression moulding process involves mixing materials, additives, and preheating. The raw materials, which can include thermosetting plastics or rubber, are often combined with various additives such as fillers, pigments, or curing agents. This mixture is then preheated to achieve a specific viscosity, making it easier to mold.
Loading the Material into the Mold
Once the material is prepared, the next step is loading the material into the mold. The mold setup typically consists of two metal plates that are heated to a specific temperature. The operator places a pre-measured charge of the prepared material into the cavity of the lower mold half. This step is critical because using too much material can lead to excess flash—unwanted overflow that requires trimming later.
Applying Heat and Pressure
After loading the material, it is time to apply heat and pressure using a compression molding machine. The mold is closed, and pressure is applied to compress the charge within the heated cavity. This pressure forces the material to flow and fill all contours of the mold, ensuring that it takes on the desired shape. The controlled application of heat and pressure is vital for achieving uniformity in the molded part and preventing defects.
Curing and Part Removal
The final stage involves curing and part removal. During this step, the heat causes chemical reactions in thermosetting materials that solidify them into their final shape. Once curing is complete, the mold opens, and the finished part is ejected. This process may involve removing any excess material or flash manually or through trimming processes. Proper demolding techniques are essential to avoid damaging the part during removal.
Different Type of Compression Molding Process
The compression molding process encompasses various types, each suited for specific applications and materials. Understanding these types and the corresponding machines is essential for manufacturers looking to optimize their production capabilities.
Standard Compression Molding
This is the most common type of compression molding, where a preheated material is placed into an open mold cavity. The mold is then closed, and heat and pressure are applied to shape the material. This method is ideal for producing simple shapes and larger components.
Transfer Molding
In transfer molding, the material is first heated in a separate chamber before being transferred into the mold cavity through a runner system. This process allows for more complex shapes and can handle materials that require precise control over temperature and pressure. Transfer molding is particularly effective for thermosetting plastics.
Injection Compression Molding Process
This hybrid process combines elements of both injection molding and compression molding. In the compression injection molding method, the molten material is injected into an open mold that is then closed to apply compression. This technique helps reduce internal stresses in the molded parts and improves dimensional accuracy, making it suitable for thin-walled applications and complex geometries.
Vacuum Compression Molding
Vacuum compression molding involves placing a preheated material into a mold cavity, similar to standard compression molding. However, before the mold is closed, a vacuum is applied to remove air from the mold cavity. This vacuum environment helps to eliminate air pockets and bubbles within the material, resulting in denser and more uniform final products.
Different Compression molding Machine
Compression Molding Presses
The primary equipment used in compression molding is the compression molding press. These machines apply the necessary heat and pressure to form the material into the desired shape. They come in various sizes and configurations, depending on the scale of production and the complexity of the parts being produced.
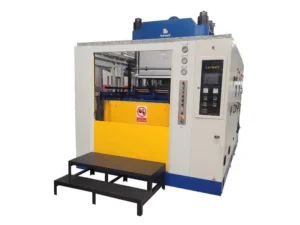
Hydraulic vs. Mechanical Presses
Hydraulic presses are commonly used in compression molding due to their ability to generate high levels of pressure with precise control. They are ideal for larger molds and thicker materials.
Mechanical presses, on the other hand, use a mechanical advantage to apply pressure and are generally faster than hydraulic presses. They are suitable for high-speed production but may not achieve the same level of pressure as hydraulic systems.

Different Compression Mold Types
In the compression molding process, the type of mold used significantly influences the efficiency, cost, and quality of the final product. There are several types of molds designed for different applications, each with its advantages and disadvantages.
Single Cavity Molds
A single cavity mold is designed to produce one part per cycle. This type of mold is particularly suitable for low-volume production or when manufacturing complex geometries that require precise control.
Advantages:
- Better control over the molding process and part quality.
- Flexibility to make adjustments or changes to the mold design or material during production.
- Ideal for prototyping or testing new designs before scaling up production.
Disadvantages:
- Higher cost per finished part compared to multi-cavity molds.
- Slower production rates, as only one part is produced at a time.
Multi-Cavity Molds
Multi-cavity molds contain two or more cavities within a single mold tool, allowing for multiple identical parts to be produced in one cycle. This design is efficient for mass production.
Advantages:
- Increased production efficiency, as multiple parts can be produced simultaneously.
- Lower cost per part due to shared tooling costs across multiple parts.
- Suitable for high-volume production runs where consistent quality is required.
Disadvantages:
- More complex design and higher initial tooling costs.
- Requires careful engineering to ensure uniform filling and cooling of all cavities.
Custom Molds for Specific Applications
Custom molds are tailored to meet specific requirements for unique products or applications. These molds can be designed as single cavity, multi-cavity, flash, positive, or semi-positive molds depending on the needs of the project.
Advantages:
- Tailored designs can optimize performance for specific materials or product shapes.
- Can accommodate specialized features that standard molds cannot handle.
Disadvantages:
- Higher development costs and longer lead times due to custom design and manufacturing processes.
Types of Custom Compression Molds
Flash Molds: These are the most common type of compression molds due to their simple structure and low manufacturing cost. They allow excess material to escape during compression, which helps control costs but may result in some material waste.
Positive Molds: More complex than flash molds, positive molds require an accurately measured charge and are used when controlling part density is critical. They are ideal for high-impact materials and applications requiring deep draws.
Semi-Positive Molds: Combining features from both flash and positive molds, semi-positive molds provide a balance between cost and performance. They allow some material escape but do not require extremely accurate charge measurements.
Compression Molding Process Material Selection
In the compression molding process, selecting the right materials is crucial for achieving the desired performance and cost-effectiveness of the final products. Various materials can be used, each offering unique properties suited for different applications.
Common Materials Used in Compression Molding
Thermosets
Thermosetting plastics are a primary choice in compression molding due to their excellent mechanical properties and thermal stability.
- Diallyl Phthalate (DAP)
- Epoxy
- Phenolic Resins
- Melamine
Thermoplastics
- High-Density Polyethylene (HDPE)
- Polyamide-imides (PAIs)
- Polyether Ether Ketone (PEEK)
Elastomers
Elastomers are often used in compression molding for applications requiring flexibility and resilience. These materials can withstand repeated deformation without permanent damage, making them suitable for seals, gaskets, and other flexible components.
Factors Influencing Material Choice
When selecting materials for compression molding, manufacturers must consider several factors:
Application Requirements
The specific requirements of the application dictate material selection. For instance, parts that need to withstand high temperatures or harsh chemicals will require thermosetting polymers with superior thermal and chemical resistance. Conversely, applications requiring flexibility may benefit from elastomers or certain thermoplastics.
Cost Considerations
Material costs play a significant role in determining the overall expense of the compression molding process. While advanced materials like carbon fiber-reinforced composites offer superior performance, they come at a higher price point. Manufacturers must balance performance needs with budget constraints to select materials that provide the best value without compromising quality.
Advantages and Disadvantages of Compression Molding
The compression molding process offers several advantages and disadvantages that manufacturers should consider when determining whether this method is suitable for their production needs.
Advantages of Compression Molding Process
Lower Tooling Costs Compared to Injection Molding
One of the significant benefits of compression molding is the lower initial tooling costs. The molds used in compression molding are generally simpler and less expensive to produce than those required for injection molding. This makes compression molding an attractive option for small to medium production runs or when prototyping new designs.
Ability to Produce Larger Parts with Thicker Walls
Compression molding is particularly well-suited for producing larger parts with thicker walls, which can be challenging for injection molding. This capability is beneficial in industries such as automotive and aerospace, where robust components are often required.
Versatility in Material Use
Compression molding can accommodate a wide range of materials, including thermosets, thermoplastics, and elastomers. This versatility allows manufacturers to select materials that best meet their specific application requirements, whether they need high strength, flexibility, or resistance to heat and chemicals.
Disadvantages of Compression Molding Process
Longer Cycle Times
One of the main drawbacks of compression molding is its longer cycle times compared to injection molding. The process requires time for heating, curing, and cooling, which can slow down production rates.
Labor-Intensive Process
Compression molding can be more labor-intensive than other molding processes, particularly during the loading and unloading phases. Manual handling of materials and parts can increase labor costs and introduce variability into the production process.
Design Guidance of Compression Molding Process
When designing parts for the compression molding process, several key considerations must be taken into account to ensure manufacturability and product quality. These factors include thickness, geometry, and surface finish requirements, as well as strategies for optimizing designs.
Optimal Wall Thickness
The design should aim for an optimal wall thickness typically ranging from 1.5mm to 6mm. While compression molding allows for variations in thickness, excessively thick walls can lead to longer curing times and increased material costs. Conversely, walls that are too thin may compromise the part’s strength and structural integrity.
Avoid Undercuts
While compression molding can accommodate recessed or protruding features, undercuts complicate the ejection process and may require additional mechanisms, such as sliders, which increase tooling costs. Designers should strive to minimize or eliminate undercuts wherever possible.
Smooth Transitions
Sharp corners and sudden changes in wall thickness should be avoided to ensure smooth material flow during the molding process. This helps achieve uniform cooling and reduces the risk of defects.
Surface Finish Requirements
Designers should consider the desired finish (e.g., matte or glossy) and incorporate appropriate texturing into the mold design. The mold surface should be prepared to achieve the required finish, as imperfections in the mold will be transferred to the final part.
Applications of Compression Molding Process
The compression molding process is widely utilized across various industries such as automotive industry, aerospace industry, electrical industry, consumer goods, industrial application etc.
Examples of Compression Molded Products:
- Gaskets and Seals: Essential for preventing leaks in automotive and industrial applications.
- Brake Pads: Commonly produced using compression molding with friction compounds.
- Electrical Insulators: Used in various electrical applications to provide safety and reliability.
- Kitchenware: Items like melamine plates, cups, and utensils are frequently manufactured through this process.
- Automotive Parts: Includes large vehicle panels, engine components, and interior trim.
- Custom Parts: Tailored solutions for specific applications in various industries.
- Rubber Components: Such as O-rings and bushings that require flexibility and resilience.

Injection Molding vs. Compression Molding
Both injection molding and compression molding are widely used manufacturing processes for producing plastic parts, but they differ significantly in their methods, applications, and efficiencies. Understanding these differences is essential for manufacturers to choose the appropriate technique for their specific needs.
Attribute | Injection Molding | Compression Molding |
---|---|---|
Raw Material Placement | Material is fed through a hopper and screw into the heated mold cavity. | Material is manually placed into the heated mold cavity. |
Pressure | High pressure applied during injection. | Pressure applied when the mold is closed. |
Heat Application | Screw heats the material while injecting it into the mold. | Preheated mold cavity and material before compression. |
Detail Complexity | Capable of producing intricate details and complex geometries. | Suited for simpler designs with larger panels. |
Production Volume | Ideal for high-volume production with fast cycle times. | Better suited for medium-volume production. |
Labor Intensity | Less labor-intensive due to automation. | More manual labor required for material placement and part removal. |
Tooling Costs | Higher initial tooling costs due to complex mold design. | Lower tooling costs compared to injection molding. |
Key Differences Between Injection Molding and Compression Molding
Material Handling and Process Flow
In injection molding, plastic resin pellets are heated and melted in a barrel before being injected into the mold at high pressure, allowing for rapid filling and precise control over part dimensions. In contrast, compression molding involves manually loading a pre-measured amount of material into an open mold, which is then closed to apply heat and pressure.
Production Speed and Efficiency
Injection molding is characterized by shorter cycle times, often taking only seconds to minutes per cycle, making it suitable for high-volume production. Compression molding typically has longer cycle times due to the need for heating, curing, and cooling processes, which can slow down overall production rates.
Part Complexity
Injection molding excels at producing complex shapes with fine details, such as intricate components used in electronics or automotive parts. Compression molding is better suited for larger, simpler parts like gaskets or seals that do not require high precision.
Cost Considerations
While injection molding has higher initial setup costs due to more complex molds and machinery, it offers lower per-unit costs at high volumes. Compression molding has lower tooling costs but may result in higher costs per part when producing smaller quantities due to longer cycle times.
Material Compatibility
Injection molding can process a wider variety of materials, including thermoplastics, thermosetting plastics, and elastomers. Compression molding primarily uses thermosets and certain elastomers, making it less versatile in terms of material selection.
Conclusion
In this comprehensive guide on the compression molding process, we explored various aspects that are crucial for manufacturers considering this method for their production needs. When deciding between injection molding and compression molding, manufacturers should carefully assess their specific production needs. By understanding the strengths and limitations of each method outlined in this guide, manufacturers can make informed decisions that align with their operational goals and enhance their competitive edge in the market. If you have any other questions, please contact us, let Jiangzhi for you to solve.