The rubber molding process has become a key technology in modern industrial production, not only widely used in automotive, aerospace and other industrial fields, but also plays an indispensable role in our daily life. Rubber product applications can be found everywhere, from car tires and sealing rings for electronic devices to kitchen utensils and children’s toys. Rubber molding technology is driving sustainable and efficient production models while meeting different needs and high quality standards. This article will delve into the development of the rubber molding process, its application areas, and how it extends from the industrial level to our daily lives.
What is Rubber Molding?
Rubber molding is a process that processes rubber raw Substance into specific shapes, sizes and physical properties. By heating and compression, rubber molded can make raw rubber or compound rubber (rubber with vulcanization agent added) fill the mold and cross-link curing, and finally obtain the desired rubber product. Rubber molding technology can meet a variety of complex shapes, accurate sizes and functional requirements, so it is widely used in automobile manufacturing, electronics, medical and health fields. Learn more what is rubber molding?
What are the Processes of Rubber Molding?
Injection molding process:
The rubber raw Substance is heated and melted by the injection machine into the mold, and cooled in the mold. This method is suitable for mass production, high production efficiency and high precision.
Extrusion molding process:
the rubber Element is extruded by the extruder, through the specific shape of the die molding, suitable for the production of rubber tubes, rubber strips and other long strip products, often used for continuous production.
Transfer molding process:
A process in which raw rubber is transferred from a preheated chamber to a mold cavity by pressure. Similar to press molding, transfer molding can better control the flow of rubber in the mold cavity, suitable for the production of complex shapes and porous rubber products. It is commonly used to manufacture rubber product with metal or fiber inserts, such as seals and electrical insulation.
Compression molding process :
The raw glue or rubber is put into the mold, and the rubber is filled in the mold cavity and cross-linked curing molding by heating and compression. Suitable for the production of complex shape rubber products, often used in small batch production. Rubber compression molding service.
Rubber Compression Process Steps and Specific Examples
Part 01: Rubber Compression Process step:
Stage 1:
Heat and warm up the mold to a certain temperature.
Stage 2:
Open the mold and put a small piece of conditioned rubber into the cavity.
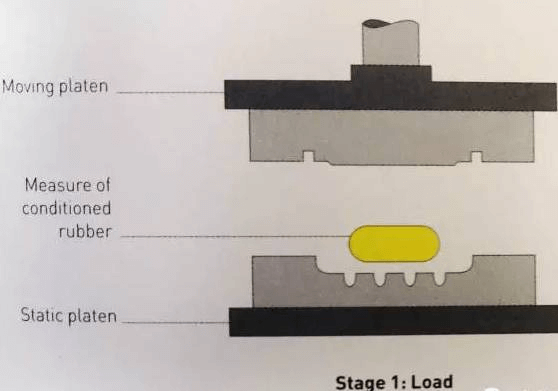
Stage 3:
The upper and lower mold plates are combined, and the rubber pieces are vulcanized and formed under high temperature and pressure.
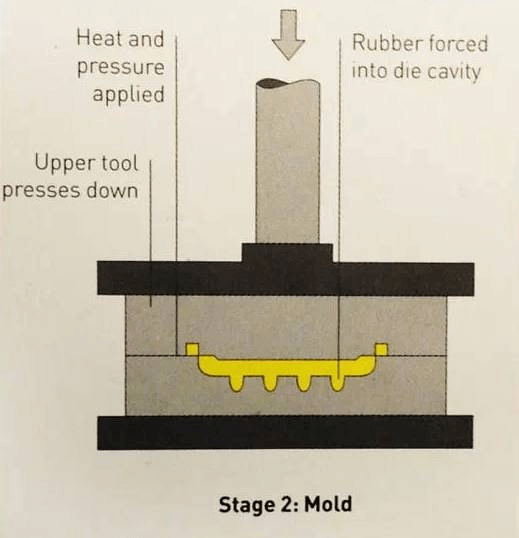
Stage 4:
Demoulding, the molded rubber products are sent to the trimming workshop.
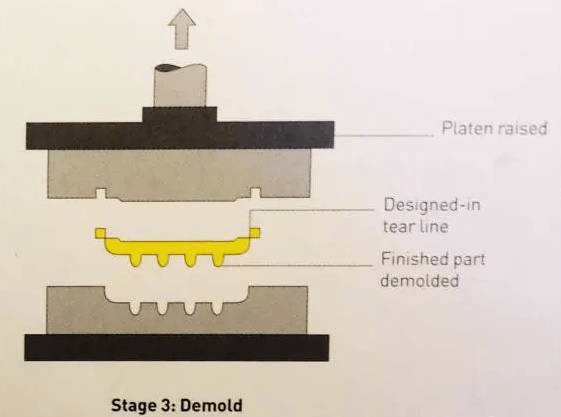
Part 02: Example: Compression-Molded Rubber Button
Step 1:
Prepare quantitative small dice of rubber.

Step 2:
Put the small dice of rubber into the cavities one by one.
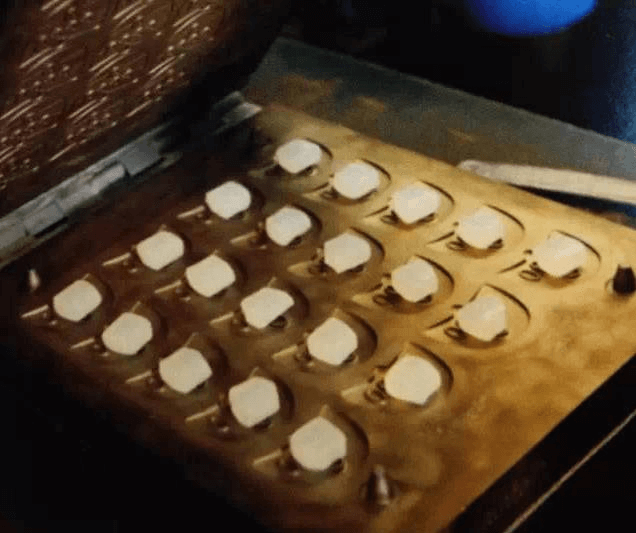
Step 3:
After heating the molds to 180°, combine the upper and lower mold plates. The rubber pieces are formed against the inner wall of the molded under high temperature and compressions and complete the molded process after 10 minutes.
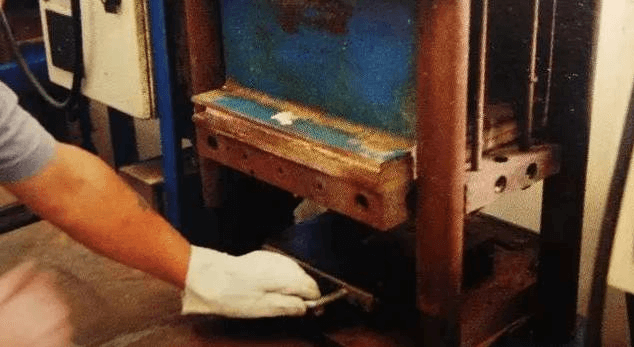
Stage 4:
Inject air into the cavities to de-mold the products.
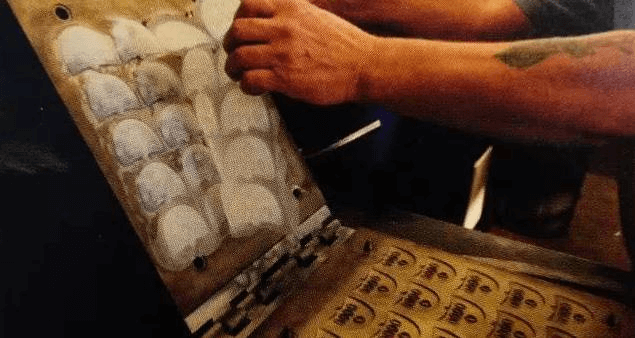
Stage 5:
Trimming and packing
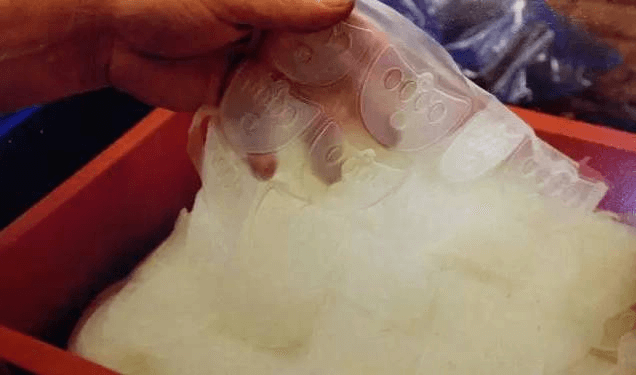
Applications of Rubber Molding Process
1. Automobile Manufacturing
- Tire: Rubber molding is the core technology of tire manufacturing, through pressure, extrusion and other forming processes to manufacture tire tread and carcass.
- Seals and shock absorbers: Rubber seals, oil seals, O-rings and other product can be used for water, dust and seal. The shock absorber absorbs vibrations through the elasticity of the rubber to enhance driving comfort.
- Hose: such as oil pipe, coolant pipe product, etc., for the transmission of various automotive fluids.
2. Electronic and Electrical Industry
- Insulation materials: Insulating skins and connector seals product for cables to provide insulation, water and dust resistance.
- Protective cover for electrical components: Rubber housing protects electronic components from external moisture, corrosion and mechanical damage.
3. Industrial Machinery
- Conveyor belt: Rubber molding conveyor belt is widely used in heavy industry such as mining, wharf and agriculture for material transportation.
- Gaskets and seals: gaskets and seals made of rubber can effectively seal liquids or gases, and are used for pipeline sealing of various industrial machinery and equipment.
- Damping pad: used to reduce the vibration of the equipment during operation and extend the mechanical life.
4. Healthcare Applications
- Medical seals and pipes: Seals made of medical grade rubber and infusion tubes, catheters, etc., used in medical equipment and infusion systems.
- Medical gloves and protective Component: Rubber formed gloves have good water resistance and puncture resistance, and are widely used in medical care.
5. Consumer Goods
- Sole: Rubber molding is an important process for sole production, with wear-resistant, anti-slip characteristics.
- Sports equipment: such as yoga mat, jump rope handle, non-slip grip, etc., rubber has a soft feel and elasticity, improve the sports experience.
- Sealing caps, household items: waterproof, dust-proof rubber sealing caps are widely used in bottle caps, container caps and so on.
6. Architecture and Civil Engineering
- Waterproof sealing material: used to seal building joints, window frames, pipe openings product, to avoid water leakage and seepage.
- Bridge shock absorber: The rubber shock absorber of the bridge can absorb shock, buffer shock, and protect the safety of the bridge structure.
7. Aerospace Applications
- Seals and insulation: Various sealing systems for spacecraft ensure the reliability of seals in high temperature, low temperature and low pressure environments.
- Shockproof materials: Aerospace equipment requires high temperature, low temperature and corrosion resistant rubber Elements as shock absorbing protection components.
With its strong adaptability, high precision and relatively low cost, rubber molded technology is widely used in many industries, providing diversified solutions for industrial production and people’s daily life. With the continuous advancement of technology, rubber molded technology will continue to promote the development of sustainable production and lay a solid foundation for future innovative applications.