The injection molding cooling system is crucial in mold design and has a great impact on the molding cycle and product quality of the product. Therefore, the uniform and reasonable design of the cooling water channel has a far-reaching impact on improving product quality and accelerating the molding cycle of the product. This chapter introduces the cooling method of the injection mould, the layout of the cooling water channel, and the general rules of the cooling system design.
Components of an Injection Mould Cooling System
Injection mold cooling systems are intricate networks designed to ensure the consistency efficiency, and quality of the final molded product. Here are the main components that up these systems:
Cooling Channels: Cooling channels are guiding the cooling medium throughout the mold. These channels ensure uniform cooling, preventing product defects and ensuring a faster cycle time.
Coolant: The most commonly used cooling mediums are water and air. Water is preferred for its excellent heat conductivity, which ensures prompt cooling and faster injection moulding cycles. Air cooling is simpler and requires less maintenance.
Heat Exchangers and Injection Molding Chillers: Heat exchangers and chillers are important for maintaining consistent mold temperatures and preventing overheating.
Pumps and Flow Regulators: Pumps and flow regulators control the pressure and flow rate of the cooling medium, ensuring it reaches every part of the mold uniformly. These components are essential for maintaining the efficiency of the cooling process and preventing hotspots within the mold.
Baffles and Bubblers: Baffles and bubblers are used to enhance cooling in difficult-to-reach areas of the mold. Baffles are cooling channels drilled perpendicular to the main cooling line, equipped with a blade that divides the cooling flow into two semi-circular paths. Bubblers function similarly, adding cooling capacity in challenging regions.
Thermal Pins: Thermal pins are used to increase the efficiency of heat transfer within the mold. They are inserted into the mold to conduct heat away from specific areas, helping to maintain temperatures and reduce cooling times.
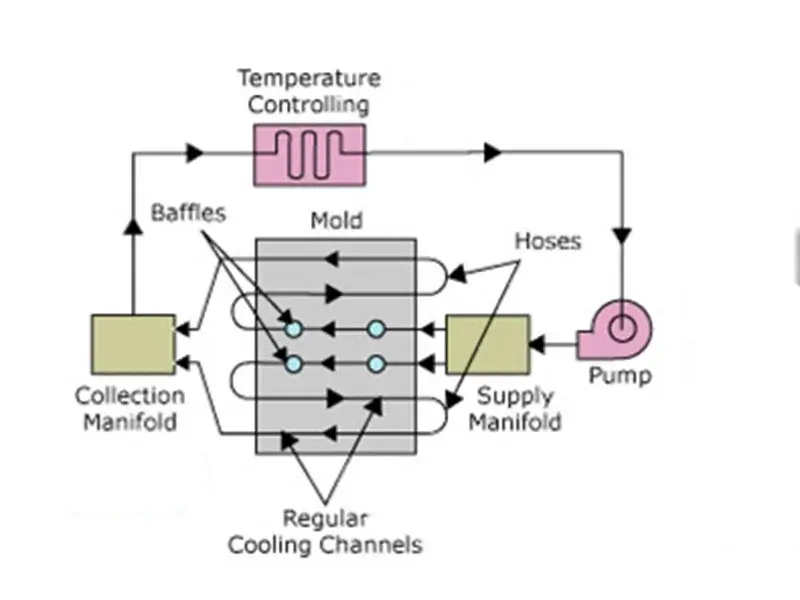
Different Types of Injection Mould Cooling Systems
1.Conformal Cooling
Conformal cooling channels are designed to follow the contour of the mould cavity, enabling even and efficient heat removal. These channels are often created using advanced manufacturing techniques like 3D printing. Conformal cooling is particularly effective for complex or large molds, providing uniform cooling and reducing cycle times.
2.Baffle and Bubbler Systems
Baffles and bubblers are used when direct cooling channels are impractical. Baffles split the coolant flow into two paths, increasing the surface area for heat exchange. Bubblers, on the other hand, are small tubes that direct coolant into deep or narrow mold areas.
3.Straight-Line Cooling Channels
These are the most basic type of cooling system, consisting of straight channels drilled into the mold. They are simple to manufacture and suitable for less complex molds. However, they may lead to uneven cooling in intricate designs.
4.Spiral Cooling Systems
Spiral cooling involves channels arranged in a spiral pattern, often used for cylindrical molds like bottle caps or containers. This configuration ensures uniform cooling around the mould.
5.Hot Oil or Hot Water Cooling
For molds processing materials that require slower cooling or precise temperature control, hot oil or hot water systems are used. These systems are particularly beneficial for heat-sensitive plastics or rubber materials.
6.Hybrid Cooling Systems
Combining different cooling methods can address specific mold design challenges. For example, a mold might use conformal cooling in critical areas and straight-line channels elsewhere, balancing efficiency and cost.
Selecting the appropriate cooling system depends on factors such as material type, mold complexity, production volume, and required cycle time.
Injection Mold Cooling System Design Principles
To improve productivity and ensure product quality, the basic principle of designing an injection mould cooling system is to ensure uniform cooling of plastic parts.
Maximize the Number and Size of Cooling Channels
The temperature of the cavity surface is closely related to the size and density of the cooling channels. Larger diameter cooling channels and smaller channel spacing result in a more uniform cavity surface temperature.

Appropriate Distance from Cooling Channels to Cavity Surface
The distance between the channel wall and the cavity surface should generally be greater than 10mm, with 12-15mm being commonly used. If too close, the cavity surface temperature becomes uneven; If too far, thermal resistance increases and cooling efficiency decreases.
For parts with uniform wall thickness, maintain the same distance between the cooling channels and the cavity surface. For parts with uneven wall thickness, place the cooling channels closer to the cavity surface near thicker walls.

Parallel Water and Material Flow to Enhance Cooling at the Gate
During molding, high-temperature plastic melt enters the cavity through the gate, causing higher temperatures near the gate and lower temperatures at the material flow’s end.
Position the cooling water inlet near the gate, ensuring that the cooling water flows in the same direction as the material in the cavity, leading to more uniform cooling.
Maintain a Small Temperature Difference Between Inlet and Outlet Water
A large temperature difference between the inlet and outlet water causes uneven mold temperature distribution. To achieve a consistent cooling speed across the product, arrange cooling channels to minimize the temperature difference between inlet and outlet water.
Reasonable Arrangement of Cooling Channels
Arrange cooling channels according to the shape of the cavity. Different plastic part shapes require different cooling channel positions for optimal cooling.
Ease of Processing and Assembly for Cooling Channels
Design the cooling water channel structure with processing technology in mind. It should be easy to manufacture, ideally using simple techniques such as drilling.
Essential Considerations for Designing Effective Cooling Systems
The design of an effective cooling system in injection moulds is critical to achieving optimal performance, product quality, and efficiency. Key factors to consider include:
1.Material Properties
The thermal conductivity and heat sensitivity of the plastic or rubber material being processed significantly influence the cooling system design. Materials with higher thermal conductivity require efficient cooling to dissipate heat quickly, while heat-sensitive materials may demand precise temperature control.
2.Mold Geometry
Complex mold shapes and intricate cavity designs require customized cooling solutions, such as conformal cooling or bubblers, to ensure uniform heat removal. The cooling system must be tailored to prevent hot spots and ensure consistent cooling across all areas.
3.Cycle Time Requirements
Cooling time often constitutes the largest portion of the injection molding cycle. Shorter cycle times demand high-efficiency cooling systems, while processes prioritizing product quality may accept slightly longer cooling durations for improved precision.
4.Coolant Flow Rate and Temperature
The flow rate and temperature of the cooling medium (water, oil, or other fluids) must be optimized to balance effective heat transfer and energy efficiency. Inadequate flow or improper temperature can lead to uneven cooling and defects.
5.hannel Placement and Size
Proper placement and sizing of cooling channels are essential for achieving uniform temperature distribution. Channels must be positioned close to the mold surface without compromising mold strength, and their size must accommodate sufficient coolant flow.
6.Thermal Simulation and Analysis
Using advanced simulation tools helps predict heat flow and identify potential issues, enabling the design of a more effective cooling system. Simulations can optimize channel placement and validate performance before mold manufacturing.
7.Maintenance and Durability
The cooling system must be easy to clean and maintain to prevent blockages or scale buildup. Durable materials should be used for components exposed to high pressures or corrosive coolants.
By carefully addressing these factors during the design phase, manufacturers can enhance cooling efficiency, improve product quality, and reduce overall production costs.
Common Issues Caused by Improper Injection Mold Cooling System
An improperly designed or maintained injection mold cooling system can lead to several issues that affect the quality of molded parts and the efficiency of the production process. This section outlines common problems and provides solutions to address them effectively.
Uneven Cooling and Warping
Cooling channels placed too far from the mold cavity, with uneven spacing, variations in coolant flow rate, or significant differences in the temperature between different parts of the mold will cause uneven cooling and warping.
Solutions:
Optimize channel placement, and ensure cooling channels are placed as close to the cavity as possible, with consistent spacing, to achieve uniform cooling.
Use temperature control units (TCUs) to regulate and maintain consistent flow rates throughout the mold.
Ensure the coolant temperature is evenly distributed across the mold by minimizing the temperature difference between inlet and outlet water.
Cooling Channel Blockage
Lack of regular cleaning and maintenance can cause particles, scale, and debris in the coolant can block the channels.
Solutions:
Implement filtration systems to remove contaminants from the coolant. Schedule regular cleaning and inspection of cooling channels to prevent blockages. Use appropriate cleaning agents to remove scale and corrosion.
Conclusion
The injection mould cooling system is a critical aspect of mold design that significantly impacts the quality of molded parts and the efficiency of the production process. Ensuring uniform and effective cooling is essential to prevent common issues such as warping, sink marks, residual stresses, and longer cycle times. A well-designed and maintained injection mold cooling system leads to higher product quality, reduced defects, shorter cycle times, and improved overall productivity.