Injection molding lifter and slider are crucial components in injection mold design. Sliders and lifters in injection molding expand the range of possible part designs, improve part quality by reducing the need for post-processing, and enable the production of complex components in a single molding operation. In this post, we will explore what are sliders and lifters in injection molding, compare the differences slider vs lifter , and design considerations.
What are Injection Molding Sliders?
Injection mold sliders are mechanical components incorporated into mold designs to enable the production of complex plastic parts with features like undercuts, side holes, or protrusions that would be difficult or impossible to mold with a basic two-part mold. Injection molding sliders are movable components in the mold that convert the vertical opening motion of the mold into horizontal movement. Their primary purpose is to form complex geometries and release the finished product upon mold opening, allowing for the creation of undercuts and other features that would otherwise prevent part ejection.
Injection mold sliders are specialized components used to release undercuts or features on molded parts that cannot be ejected using standard methods. They move horizontally (or at an angle) within the mold, typically driven by angled pins or cam systems. Sliders are commonly used for side holes, slots, or overhangs on parts. Their design requires precise alignment to ensure smooth movement, making them essential for creating complex geometries in injection molding.

Common Applications of Sliders in Injection Molding:
Sliders are commonly used for parts with:
- Undercuts
- Side holes or grooves
- Clips
- Windows
- Any features that prevent straight ejection from the mold
Components of a Slider Mechanism:
A typical slider system consists of:
- Slider base
- Slider insert
- Press block
- Wedge
- Angle pin (guide pin)
- Wear plate
- Stopper bolt
- Springs
Injection Molding Sliders Working Principle:
The slider’s motion is powered by the angled guide pin, which converts the vertical mold opening/closing movement into horizontal motion.
During mold closure, the slider moves into position to form the desired feature (e.g., undercut). When the mold opens, the angled guide pin causes the slider to retract horizontally, releasing the undercut or complex feature. This horizontal movement occurs before or simultaneously with the mold opening, allowing the part to be ejected without damage. The wedge component prevents the slider from retracting during injection due to pressure.
Locking mechanisms (like KOR-LOK systems) can be used to maintain the slider’s position and prevent unwanted movement during molding.
What are Injection Molding Lifters?
Injection mold lifters are specialized components used in injection mold design to enable the production of parts with internal undercuts or complex internal geometries. Lifters are angled mechanisms that provide both vertical and horizontal motion as the mold opens. Their primary purpose is to form and release internal undercuts or features that require a more complex ejection path than a straight pull can provide.
Injection molding lifters are components designed to release undercuts or internal features on molded parts that cannot be ejected directly. Unlike sliders, lifters move both vertically (in line with the mold opening direction) and at an angle, making them ideal for features like internal hooks, clips, or threads.
Lifters are typically driven by the ejector plate and require careful design to ensure smooth operation and prevent part damage. They are essential for producing parts with complex internal geometries while maintaining high precision and efficiency during molding.
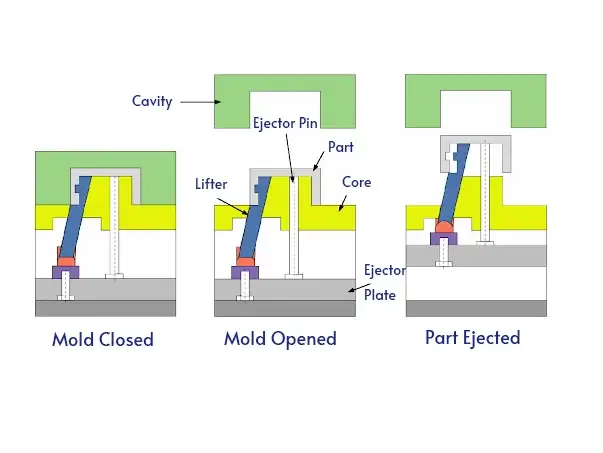
Common Applications of Injection Molding Lifters
Lifters are commonly used for parts with:
- Internal undercuts
- Ribs or bosses with no draft
- Complex internal geometries
- Features that prevent straight ejection from the mold
Components of a Lifter Mechanism
A typical lifter system consists of:
- Lifter body (blade-like or pin-like)
- Ejector plate
- Retainer plate
- Locking mechanism (block-like)
- Angled locating block
- Ejector pins (optional)
Injection Molding Lifters Working Principle
The lifter is incorporated into the mold closure and opening mechanism at an angle. During mold closure, the lifter moves into position to form the desired internal feature. When the mold opens, the ejector plate pushes the lifter upward and at an angle. This angled movement allows the lifter to retract from the internal undercut while simultaneously pushing the part upward. The distance the lifter moves corresponds to the internal undercut geometry. An ejector pin may be used to ensure the part doesn’t remain on the lifter after ejection.
The lifter’s motion is controlled by the action of the injection molding press pushing against the ejector plates, rather than using an angled pin like sliders do.
Lifters can be categorized as integral (single unit) or non-integral (two separate units). Integral lifters are typically used for smaller parts, while non-integral lifters are better suited for larger parts. The shape of lifters can also vary, with cylindrical lifters being simpler and more common, while T-shaped lifters are used for larger parts requiring higher precision.
Injection Molding Lifters Product Advantage
- High efficiency: lifter can quickly and efficiently complete the complex stripping process and shorten the production cycle.
- High precision: lifter’s precision manufacturing ensures that parts are deformable and flawless when demoulded.
- Versatility: Suitable for a variety of mold design needs, can be flexibly applied in different production environments.
- Durability: Use of high-strength materials and optimized design to increase lifter life in high frequency use.
- Cost effective: Although the initial investment is high, long-term use reduces the overall production cost due to reduced downtime and scrap rates.
Injection Molding Lifter Common Problems Solutions
- Problem: Plastic parts surface damage or drag marks
Solution: Use highly machined skew pins and surface smoothing treatments (such as chrome plating) to reduce friction resistance while adjusting mold clearance. - Problem: lifter wears out easily
Solution: Use wear-resistant materials (such as heat-treated steel) and add lubrication systems or coatings (such as DLC coatings) to key parts of the lifter. - Problem: The reset is not accurate, affecting the next injection molding
Solution: Optimize lifter’s guiding mechanism, add spring or hydraulic power to improve reset accuracy.
Struggling with Undercuts, Complex Geometries, or Ejection Failures?
What are the Differences Between Injection Molding Slider and Lifter?
What is the difference between lifter and slide in injection molding? Injection molds often include specialized mechanisms like sliders and lifters to address complex part geometries and facilitate mold release. While both components are used to release undercuts and ensure smooth part ejection, they differ significantly in structure, functionality, and applications. Here’s a detailed comparison:
1. Functionality
- Slider:
A slider is a moving component within the mold that slides horizontally (or at an angle) to release undercuts or features that cannot be demolded by standard ejection methods. It is typically actuated by an angled pin or cam system during the opening of the mold.
Example Use: Side holes, slots, or overhangs. - Lifter:
A lifter moves in a combination of vertical and angular directions to release undercuts that are on the interior surfaces of the mold cavity. Lifters are usually driven by the motion of the ejector plate.
Example Use: Internal threads, clips, or hooks.
2. Movement Direction
- Slider:
Primarily moves horizontally (or at an angle perpendicular to the mold opening direction). - Lifter:
Moves both vertically (in line with the mold opening direction) and at an angle to accommodate undercuts.
3. Applications
- Slider:
Best suited for external or side features. It is commonly used in molds where the undercut is located on the outer surfaces of the part, making side movement essential. - Lifter:
Ideal for internal features or deep undercuts where vertical lifting and a small angular offset are required. It is often used for parts with complex geometries requiring precise ejection.
4. Design Complexity
- Slider:
The design of a slider mechanism is generally more complex, involving cams, guide rails, and precise alignment to ensure smooth horizontal movement. This complexity can increase the mold cost and maintenance requirements. - Lifter:
Although simpler than sliders, lifters require careful design to balance the vertical and angular movement, ensuring they can clear the undercut without damaging the part or mold.
5. Cost and Maintenance
- Slider:
Due to its intricate mechanism and reliance on additional components, sliders are typically more expensive to design, manufacture, and maintain. - Lifter:
Lifters are less costly compared to sliders, but their design must account for potential wear and tear from frequent angular movement during ejection.
6. Operational Constraints
- Slider:
Requires adequate mold space for the cam system and horizontal movement. It may not be feasible for molds with limited room or small parts. - Lifter:
Limited by the angle of movement and the complexity of the internal features. Lifters may face issues with alignment or sticking if not designed correctly.
While both sliders and lifters in injection molding play crucial roles in addressing undercuts and enabling smooth demolding, their selection depends on the part’s geometry, mold space, and production requirements. Sliders excel in handling external or side features, whereas lifters are better suited for internal geometries. A thorough understanding of these mechanisms ensures efficient mold design and high-quality part production.
Conclusion
Although injection mold slider and lifter use come with challenges, they significantly expand the possibilities in plastic part manufacturing. They enable the creation of complex geometries and intricate features that would be impossible with standard molds, improving part quality and reducing post-processing needs. As plastic part designs continue to evolve, the importance of sliders and lifters in injection molding is likely to grow. When implemented effectively, these mechanisms significantly enhance a manufacturer’s ability to produce high-quality, complex parts that meet modern industry demands.
FAQs About Injection Molding Slider and Lifter
While both lifters and ejector pins serve the purpose of part ejection in injection molding, lifters are specifically designed for complex internal geometries and undercuts, providing angled movement, whereas ejector pins are used for straightforward ejection with vertical movement.
In high temperature injection molding, the sliders and thimbles ensure smooth removal of parts with complex shapes or side depressions. High temperature materials such as PEEK, PTFE, etc., often have high viscosity and difficult to form, and the design of the slide and thimble is crucial to ensure the smooth release of the part.
Hardened steel: Common and durable, suitable for most high temperature applications.
Tool steel (such as H13) : H13 steel has excellent high temperature resistance and is commonly used in high temperature injection molds.
Titanium alloy: high strength, high heat resistance, but high cost, often used in applications requiring extremely high strength and heat resistance.
Superalloys: such as Inconel, are suitable for applications at extremely high temperatures and are commonly found in aerospace and special industries.