Injection molding undercuts is one of the most significant challenges. Types of undercut in injection molding prevent molded parts from ejecting from the mold in a straight line.In this post, we’ll explore the concept of injection mold undercuts in-depth, discussing their types, challenges, and various solutions for effectively incorporating them into part designs.
What Are Injection Molding Undercuts?
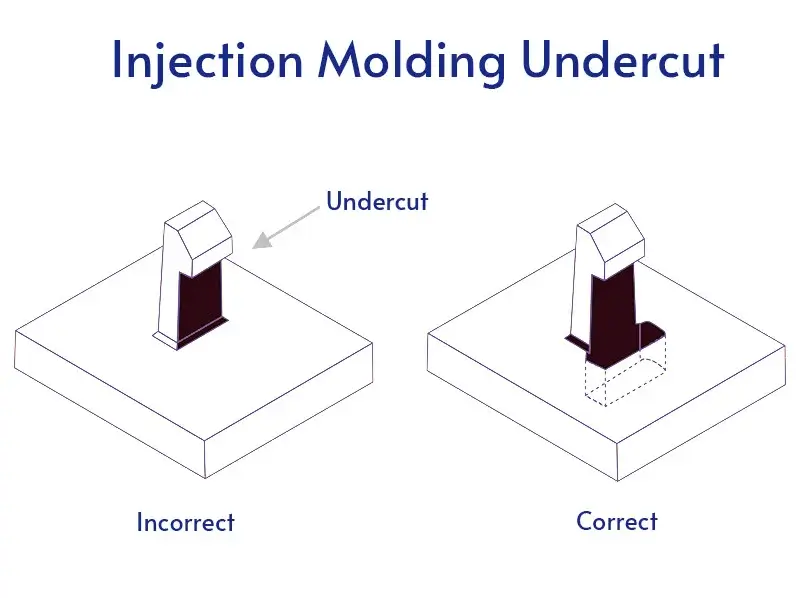
Injection molding undercut is a feature on a molded part that prevents the straightforward removal of the molded piece from the mold due to its geometry. These features typically involve protrusions or recesses that catch on the mold during ejection, complicating the demolding process. Undercut in plastic design are significant because they require special design considerations to ensure the part can be removed without damage.
Two Main Types of Undercuts in Injection Molding
Undercuts can be classified into two main types:
-
- External undercuts: These are features on the exterior of the part that prevents straight ejection. Snap fits, or hooks that extend beyond the parting line of the mold.
- Internal undercuts: These are features on the interior of the part that cannot be captured from the outside. Such as internal threads, holes, or slots that interfere with direct ejection.
Injection Molding Undercts Examples
Common examples of undercut in plastic design include:
- Threaded components: Vertical threads on bolts, nuts, or other fasteners create undercuts.
- Snap-fit features: Interlocking designs used to connect two parts without screws often involve undercuts.
- Side holes: Holes on the side of a part that serve design or functional purposes create undercuts.
- Barb fittings: Often used in medical devices, these require undercuts to form a lip that holds the mating part.
- Custom inserts: Undercuts can be used to accommodate inserts that fit into larger parts.
- Clamshell or housing designs: These often incorporate interlocking or snap and latch features that require undercuts.
- Button features and ports for wiring: These often create undercuts on consumer electronics housings.
What is the Function of the Injection Molding Undercut?
Undercuts in injection molding serve several important functions, enhancing the design and functionality of molded parts. Here are the key roles that undercuts play:
1. Interlocking Mechanisms in Injection Mold Undercut
Undercuts allow for the creation of interlocking features within molded parts. This enables designs such as snap-fit closures and hinges, which facilitate secure assembly without additional hardware or adhesives. For example, bottle caps and electronic device components often utilize undercuts for effective sealing and assembly.
2. Enhanced Functionality in Injection Molding Undercuts
By incorporating undercuts, designers can improve the functionality of parts. Features like gripping surfaces or textured areas can be created, enhancing usability and ergonomics for tools and consumer products.
3. Aesthetic Appeal in Injection Mold Undercut
Undercuts contribute to the visual complexity and sophistication of a product’s design. They can differentiate products in competitive markets, making them more visually appealing to consumers.
4. Material Efficiency in Injection Mold Undercuts
Undercuts can optimize material usage by allowing for thinner walls or less material-intensive structures while maintaining structural integrity. This can lead to cost savings in material costs.
5. Streamlined Assembly in Injection Molding Undercuts
Parts designed with undercuts can simplify the assembly process by allowing for easier mating of components, reducing assembly time and complexity. This efficiency contributes to more cost-effective manufacturing.
When to Incorporate Undercut Features in Your Design
Here are some key situations that make undercuts necessary in injection molding:
- Custom inserts: Undercuts allow for creating custom inserts that fit into larger parts. This is often used in medical devices or products needing an exact fit. Undercut inserts can also serve as alternatives to screws or rivets for attaching parts.
- Side holes: Undercuts enable the creation of side holes that are difficult to produce using traditional methods. Side holes are used for mounting components, attaching parts to other equipment, or for aesthetic/venting purposes.
- Vertical threads: Undercuts are necessary for molding vertical threads, commonly found on bolts and screws. These are also used in assemblies where multiple parts need to thread together.
- Barb fittings: The male parts of barb fittings require undercuts to form a lip that holds the female mating part.
- Interlocking features: Designs with interlocking elements like tongue and groove connections require undercuts on one side to allow mating with the other part.
- Snap fits: Undercuts are essential for creating snap fit features that allow parts to connect without screws.
- Hooks and latches: These features often require undercuts to function properly.
- Internal geometries: Complex internal shapes may necessitate undercuts to be properly formed.
Injection Molding Undercuts Design Strategies
To effectively manage undercuts in injection molding, several design strategies can be employed. Each of these strategies aims to simplify the ejection process while accommodating the complexities introduced by undercuts. Here’s the key strategies:
Adjusting the Parting Line
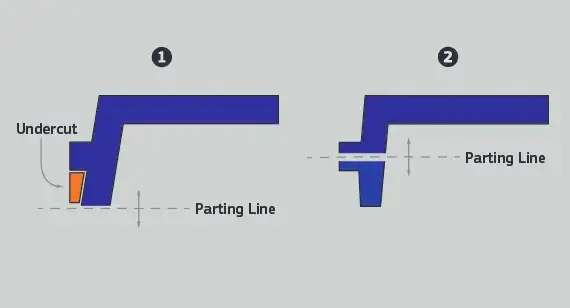
Moving the parting line of the mold to intersect with the undercut is often the simplest solution for external undercuts. By strategically placing the parting line, you can minimize the need for additional mechanisms, making the mold design simpler and potentially reducing production costs. This adjustment allows for smoother ejection of the part since the undercut feature can be directly accessed during the mold opening process.
Using Side Actions

Side action cores are movable inserts that slide into the mold during the closure phase and retract before the mold opens. This mechanism is essential for creating undercuts that would otherwise prevent the part from being ejected. Side actions must move perpendicular to the mold’s opening direction, which can complicate the design but is necessary for achieving intricate external geometries. This method can significantly reduce mold complexity and enhance the ability to produce detailed parts.
Implementing Lifters in Molding Undercut Design
Lifters are mold components that shift specific features of a part during ejection. They work by moving at an angle to pull the cavity steel away from the undercut feature, allowing for easier removal of the part from the mold. Lifters are particularly useful for internal undercuts or complex geometries, and their incorporation can streamline the ejection process while maintaining the integrity of the part.
Incorporating Draft Angles in Mold Undercuts Design
Draft angles are essential for facilitating the ejection of parts from the mold. A common guideline is to include a draft angle of about one degree for every inch of cavity depth. This tapering on the vertical walls of the part reduces friction during ejection, making it easier to remove parts with undercuts. Ensuring adequate draft angles, especially near undercut areas, is crucial for successful demolding.
Employing Bump-offs in Mold Undercut Design
Bump-offs are designed to allow parts to deform slightly during the ejection process, aiding in the release of undercut plastic injection molding features without damaging the part. This technique can simplify mold designs by reducing the need for complex mechanisms. Bump-offs are particularly effective for parts with internal undercuts, as they leverage the material’s flexibility to ease the ejection process.
Using Hand-Loaded Inserts in Mold Undercut Design
Hand-loaded inserts are components that are manually placed into the mold before the injection process begins. This technique allows for the creation of complex features without incorporating them directly into the mold design. By preventing plastic from entering certain areas, hand-loaded inserts can simplify the mold design and facilitate easier removal of parts with undercuts. This method is especially useful for low-volume production runs or prototypes.
Conclusion
Injection molding undercuts present both challenges and opportunities in plastic part design and manufacturing. While they can complicate the molding process, undercut in plastic design are often essential for creating complex geometries and functional features. By mastering injection molding undercuts design considerations and challenges, manufacturers can expand their capabilities to produce more complex and functional parts while maintaining efficiency and cost-effectiveness. As plastic part designs continue to evolve, the ability to successfully manage undercuts will remain a valuable skill in the injection molding industry